
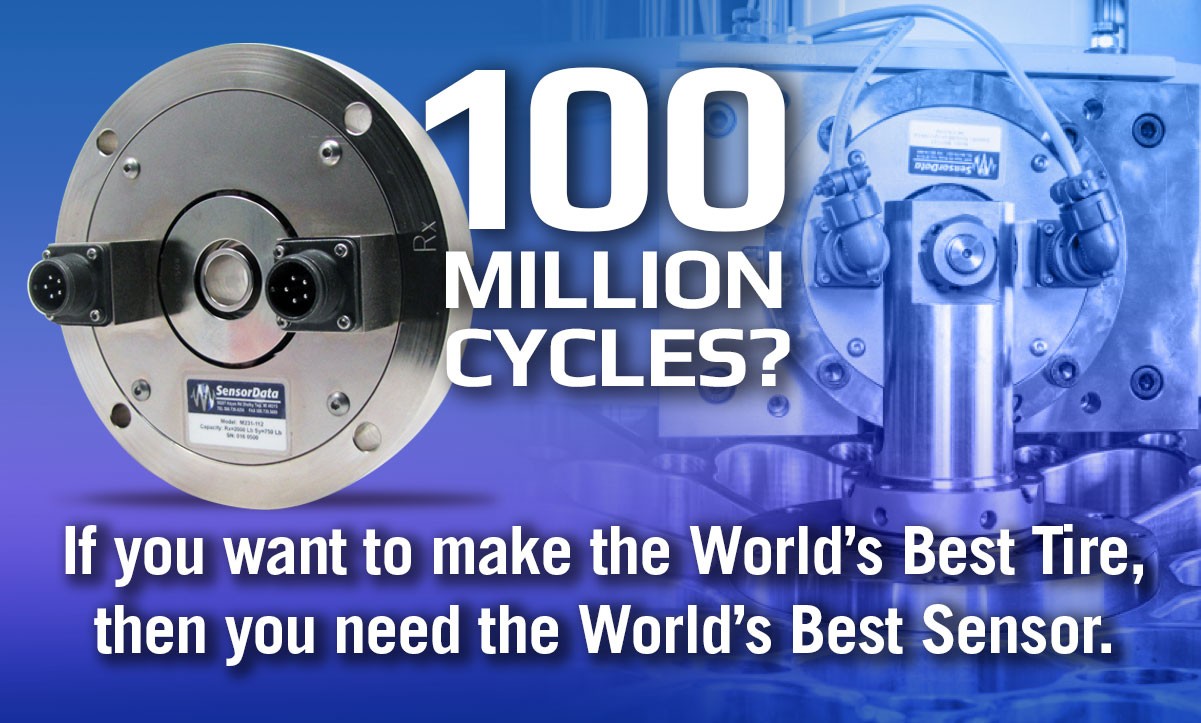
GENERAL PURPOSE vs.
FATIGUE DESIGN OF SENSORS:
The first tool out of the bag of tricks of any design engineer is the stress/strain diagram Fig.1. This curve defines the micro deformation of materials under different loads.
This tool first and foremost guides engineers to the material most suitable for the application the sensor could be used in (external forces, loading conditions, etc…).
All general purpose sensors are successfully designed based on this stress diagram, given loading is not cyclic.
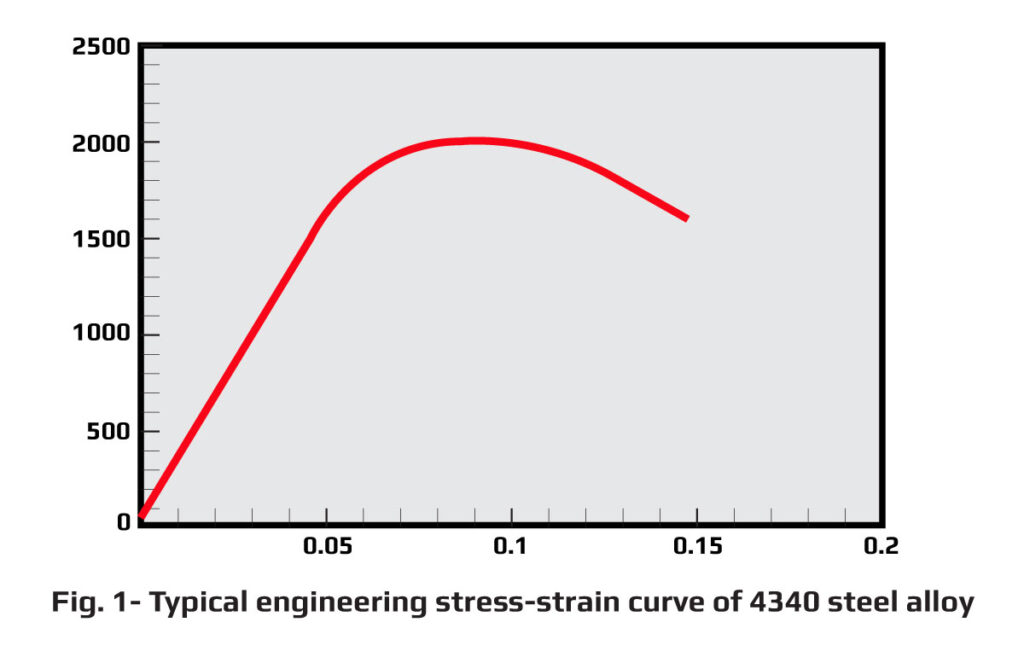
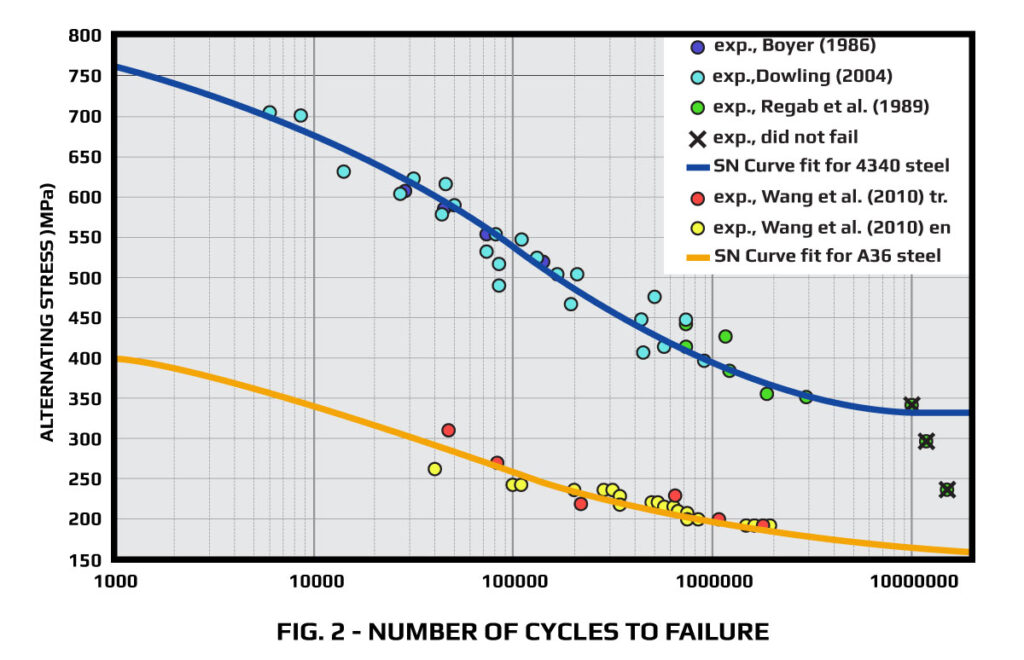
GENERAL PURPOSE vs.
FATIGUE DESIGN OF SENSORS:
In cyclic loading -also called fatigue loading- another equally important tool is required; the S/N diagram (Fig.2). This diagram identifies limiting stresses if a sensor were to survive a certain number of loading cycles without failure.
A favorable material for sensor manufacturers is the AISI 4340 alloy steel. Both Fig.1 & Fig.2 are for this alloy. Fig. 2 also includes the behavior of A36 steel under cyclic loading.
From Fig.1, this alloy provides a useful linear design range for up to 1500 MPa. But if the sensor were to survive 100,000,000 cycles, the max stress it would be loaded to should not exceed 300 MPa from Fig. 2. Notice that for the same 300 MPa, A36 steel can only survive 30,000 loading cycles. In addition to showing why 4340 is a favorable material, this also shows emphatically why designing for general purpose and designing for fatigue, are completely two different processes.
Fatigue rated load cells are specifically designed for component durability and fatigue test machines where highly cyclical loading is present. …
All fatigue rated load cells are guaranteed against fatigue failure for 100 million fully reversed cycles.
They are used for material testing, component life cycle testing and structural testing. All fatigue rated load cells are guaranteed against fatigue failure for 100 million fully reversed cycles.
SDT has several field proven fatigue rated sensors, please refer to our website for some of those models.
M231 - TIRE UNIFORMITY
Both tire and vehicle manufacturers seek to improve tire uniformity in order to improve vehicle ride comfort.
Tire manufacturers require testing machines to measure certain uniformity parameters. The number of possible uniformity tests is extensive; the ones of interest are discussed below.
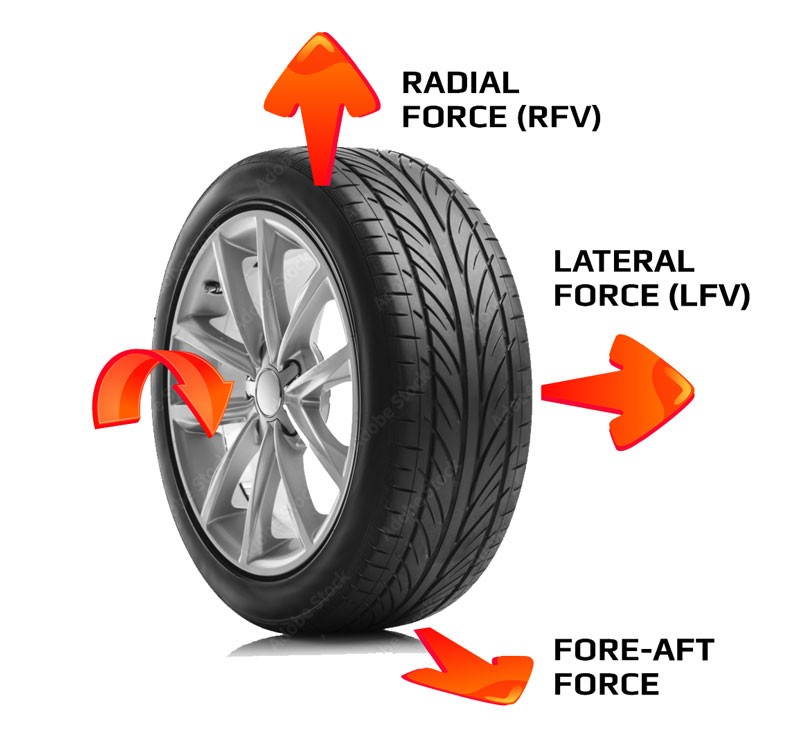
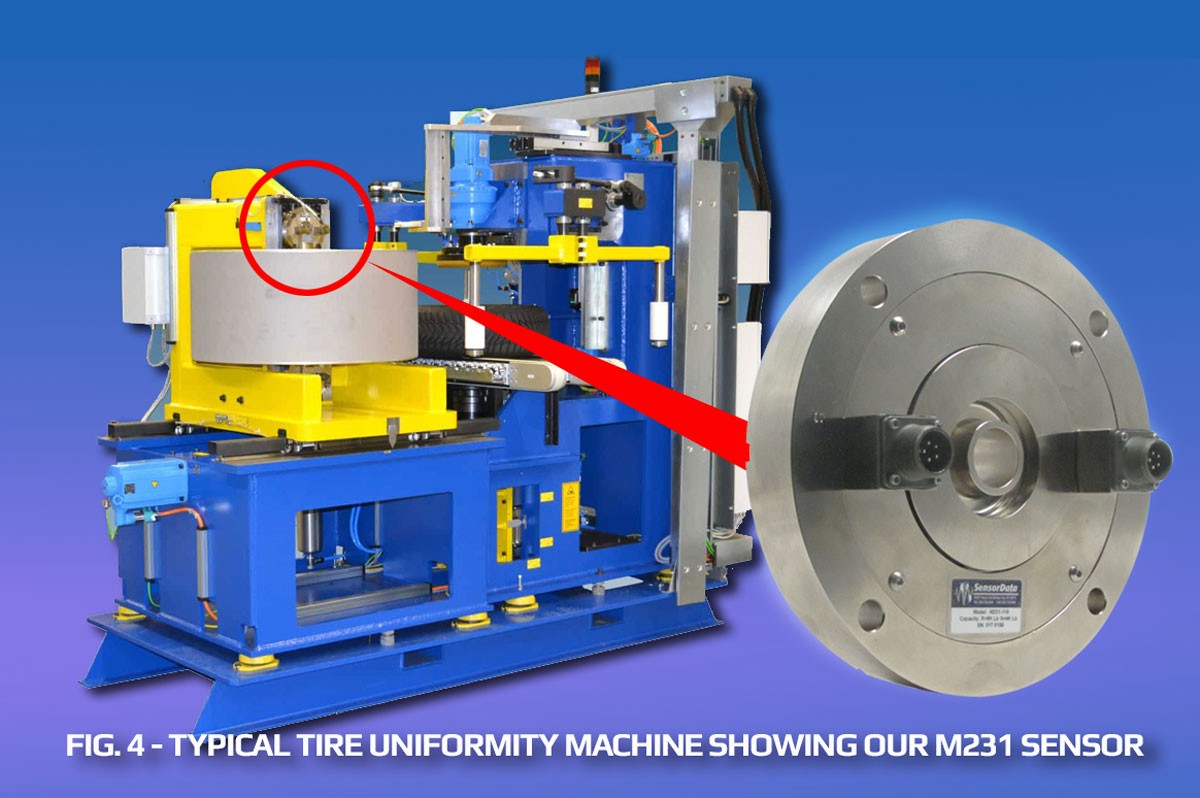
Tire Uniformity Grading Machine
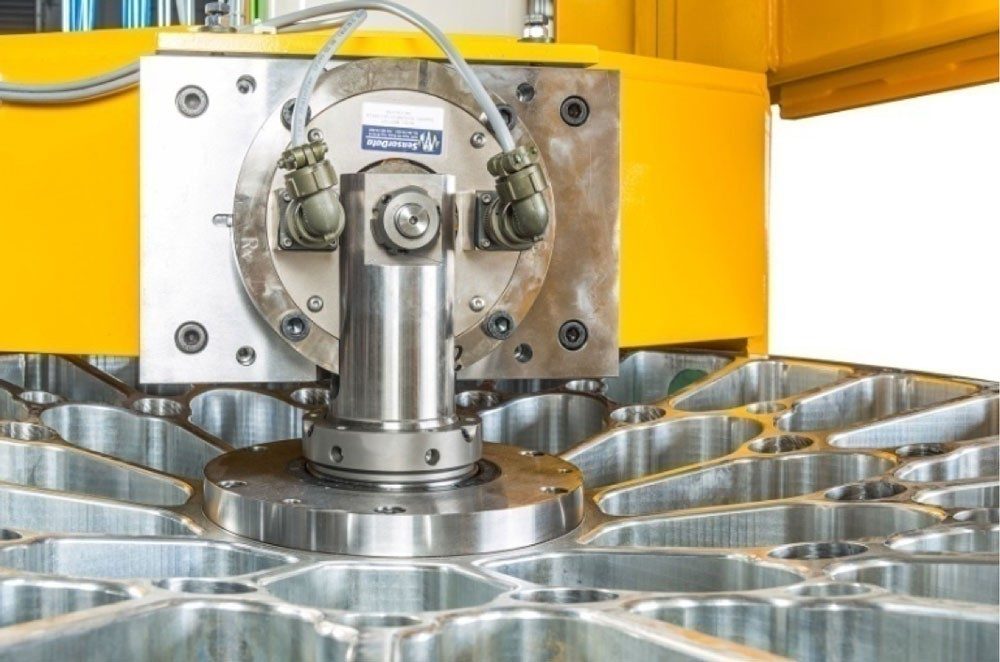
Another tire uniformity machine by a major European manufacturer showing Sensordata M231
M231 - UNIQUE FEATURES
SD manufactures two different sizes of the M231;
· Ø7.000 in capacities from 0.50 k/Lb to 2.0 k/Lb. and,
· Ø9.000 in capacities from 15kN to 60kN and from 4k/Lb to 8k/Lb
· 0.1 accuracy class
Options;
· High overload
· Tight tolerances
· available as 3-component
· available as 0.05 accuracy class
Dimensions;
SD is the first to offer this model in 60kN.
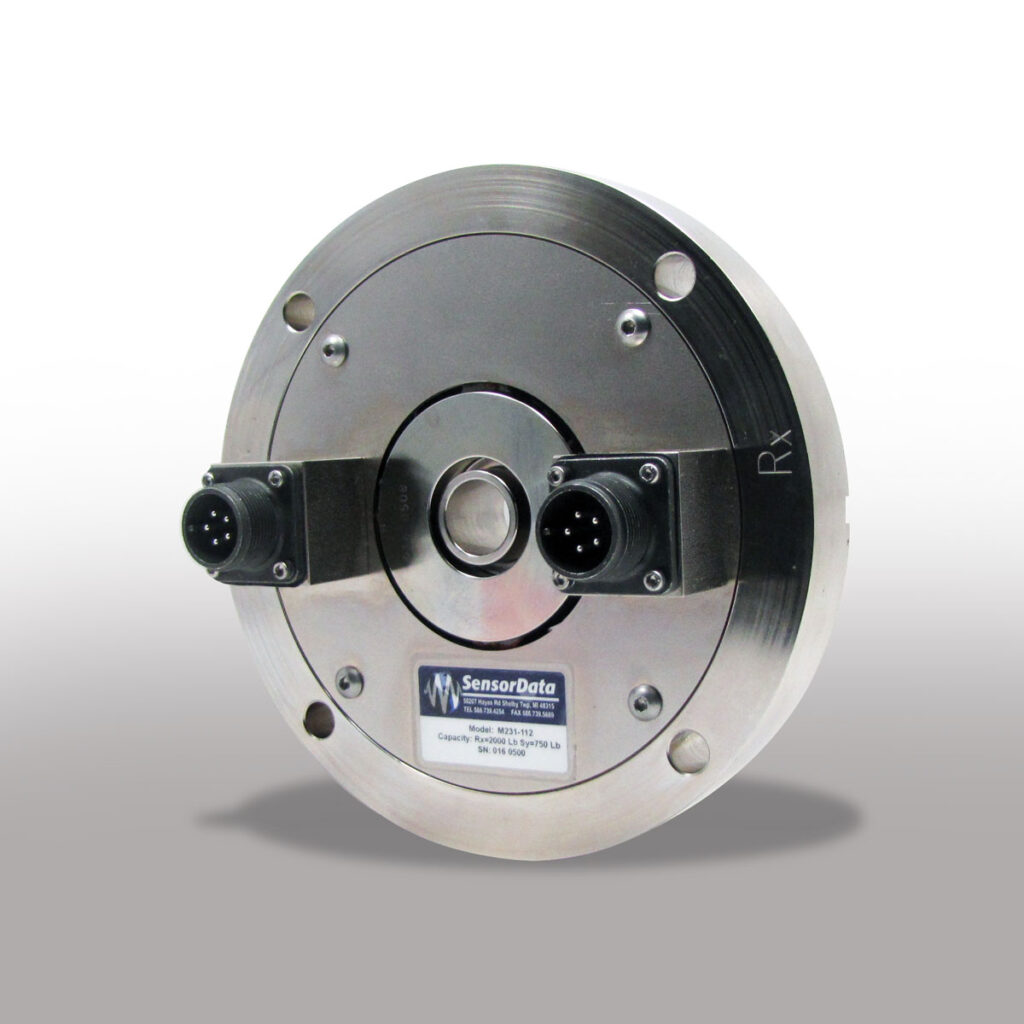
NEW AT SENSORDATA
Need a Quote?
We love helping our clients excel. We are happy to discuss your sensor requirements and provide ideas on how you can become more competitive, productive and profitable with SDT products.
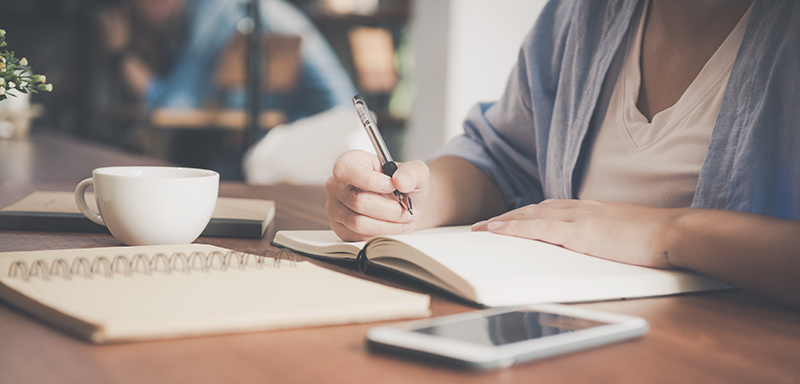