PRODUCTS
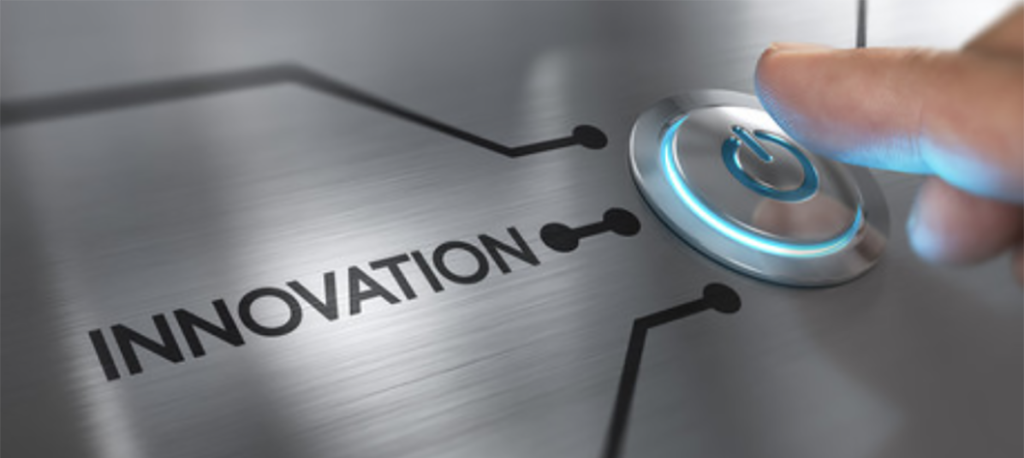
Transverse Load Apparatus
Abstract: A loading device is provided, including a first member, a second member, a first clamping member, a second clamping member, and an actuator. The first member includes a first surface, where the first surface contacts a first side of a test piece. The second member includes a second surface, for contacting a second side of the test piece. The first clamping member includes a first clamping surface for contacting the second side of the test piece. The second clamping member is fixedly secured to the second member. The actuator exerts a predetermined force driving the second member in a first direction away from the first member, and a second direction towards the first member. This force sensor, specifically crafted for the MAHLE Group GmbH, answers the need for a device that simulates the loading conditions that may occur at the crankshaft end of a connecting rod during operation of a reciprocating engine. Sensor designs undergo strict testing from our research and development team at our in-house warehouse facility in Shelby Township, Mich. All of our standard and wireless sensors are fully traceable through NIST.
Type: Grant
Filed: January 11, 2010
Issued: October 2, 2012
Assignee: Mahle International GmbH
Inventors: Roger A. Krause, Christopher Hall, Sherif Gindy
Transverse Load Apparatus
Abstract: A loading device is provided, including a first member, a second member, a first clamping member, a second clamping member, and an actuator. The first member includes a first surface, where the first surface contacts a first side of a test piece. The second member includes a second surface, for contacting a second side of the test piece. The first clamping member includes a first clamping surface for contacting the second side of the test piece. The second clamping member is fixedly secured to the second member. The actuator exerts a predetermined force driving the second member in a first direction away from the first member, and a second direction towards the first member. This force sensor, specifically crafted for the MAHLE Group GmbH, answers the need for a device that simulates the loading conditions that may occur at the crankshaft end of a connecting rod during operation of a reciprocating engine. Sensor designs undergo strict testing from our research and development team at our in-house warehouse facility in Shelby Township, Mich. All of our standard and wireless sensors are fully traceable through NIST.
Type: Grant
Filed: January 11, 2010
Issued: July 14, 2011
Inventors: Roger A. Krause, Christopher Hall, Sherif Gindy
Conveyor diagnostic system having local positioning system
Abstract: A conveyor diagnostic system for monitoring loading of a conveyor line assembly including at least one sensor component coupled to the conveyor line assembly. The sensor component is adapted for detecting loading of the conveyor line assembly and is further adapted for generating and transmitting a signal that is correlative of the loading of the conveyor line assembly. The conveyor diagnostic system also includes a ground station adapted to receive and process the signal that is correlative of the loading of the conveyor line assembly. Furthermore, the conveyor diagnostic system includes a local positioning system that is adapted for detecting the location of the sensor component in relation to a reference point. A method of using the conveyor diagnostic system is also disclosed. The aforementioned invention was developed for the Chrysler LLC automobile company. The sensor relates generally to a conveyor diagnostic system and, more specifically, to a conveyor diagnostic system having a local positioning system. Sensor designs undergo strict testing from our research and development team at our in-house warehouse facility in Shelby Township, Mich. All of our standard and wireless sensors are fully traceable through the NIST.
Type: Grant
Filed: September 9, 2005
Issued: November 13, 2007
Assignee: Chrysler LLC
Inventors: Sayed Nassar, Gerry Grzadzinski, Sherif Gindy
Conveyor diagnostic system having local positioning system
Abstract: A conveyor diagnostic system for monitoring loading of a conveyor line assembly including at least one sensor component coupled to the conveyor line assembly. The sensor component is adapted for detecting loading of the conveyor line assembly and is further adapted for generating and transmitting a signal that is correlative of the loading of the conveyor line assembly. The conveyor diagnostic system also includes a ground station adapted to receive and process the signal that is correlative of the loading of the conveyor line assembly. Furthermore, the conveyor diagnostic system includes a local positioning system that is adapted for detecting the location of the sensor component in relation to a reference point. A method of using the conveyor diagnostic system is also disclosed. The present force sensor invention overcomes the disadvantages of the related art in a conveyor diagnostic system for monitoring loading of a conveyor line assembly. Sensor designs undergo strict testing from our research and development team at our in-house warehouse facility in Shelby Township, Mich. All of our standard and wireless sensors are fully traceable through the NIST.
Type: Grant
Filed: September 9, 2005
Issued: March 15, 2007
Inventors: Sayed Nassar, Gerry Grzadzinski, Sherif Gindy
Conveyor diagnostic system
Abstract: Apparatus for measuring a plurality of forces acting on a conveyor chain of a conveyor line includes a pre-selected chain link coupled to the conveyor chain, and a sensor array having a plurality of strain gauges disposed on the pre-selected chain link, each of the plurality of strain gauges being distinctly oriented to measure the plurality of forces acting on the pre-selected link. The present strain gauge invention was developed for the Chrysler automobile company. Strain gauge application relates generally to a conveyor diagnostic system, and more particularly to a system that employs a method for measuring multi-directional forces acting on a conveyor chain. Sensor designs undergo strict testing from our research and development team at our in-house warehouse facility in Shelby Township, Mich. All of our standard and wireless sensors are fully traceable through the NIST.
Type: Grant
Filed: June 2, 2003
Issued: March 15, 2005
Assignee: DaimlerChrysler Corporation
Inventors: Sayed Nassar, Gerry Grzadzinski, Sherif Gindy
Conveyor diagnostic system
Abstract: Apparatus for measuring a plurality of forces acting on a conveyor chain of a conveyor line includes a pre-selected chain link coupled to the conveyor chain, and a sensor array having a plurality of strain gauges disposed on the pre-selected chain link, each of the plurality of strain gauges being distinctly oriented to measure the plurality of forces acting on the pre-selected link. The present strain gauge invention relates generally to a conveyor diagnostic system, and more particularly to a system that employs a method for measuring multi-directional forces acting on a conveyor chain. Sensor designs undergo strict testing from our research and development team at our in-house warehouse facility in Shelby Township, Mich. All of our standard and wireless sensors are fully traceable through the NIST.
Type: Grant
Filed: June 2, 2003
Issued: December 2, 2004
Inventors: Sayed Nassar, Gerry Grzadzinski, Sherif Gindy
Mechanical Switching Means for Providing Shunt Calibration in a Rotary Transformer System
Abstract: A system for calibrating a strain gage transducer mounted on a rotating member comprising a mechanical switch capable of making contact from a stator to selected terminals on the rotor to provide both positive and negative shunt calibration of the transducer. In a first embodiment, calibration is carried out while the rotor is stationary, providing a simple, cost effective calibration system for most applications. In a second embodiment, special terminals permit contact while the rotor is in motion. In a third embodiment, simultaneous calibration and gage measurements are possible while the rotor is in motion providing a means of continuous correction which is especially advantageous in applications where the rotor is subject to a rapidly changing environment. This strain gauge invention was developed for the Eaton Corporation relating to shunt calibration systems for transducers and, more particularly, to improvements in such systems in which rotary transformers are used to couple excitation and signal to and from a transducer mounted on a rotating member. Sensor designs undergo strict testing from our research and development team at our in-house warehouse facility in Shelby Township, Mich. All of our standard and wireless sensors are fully traceable through the NIST.
Type: Grant
Filed: November 26, 1982
Issued: January 28, 1986
Inventors: Kish Amlani, Sherif Gindy
Calibrating Device for Load Cells
Abstract: This invention relates generally to a device for calibrating a load cell such as a strain gauge and more particularly to a device adapted to provide a calculable force for calibrating the load cell arising from amplification of fluid pressure provided by standardized dead weights. Extensive research and development yielded a superior solution for power management conglomerate Eaton Corporation. Sensor designs undergo strict testing from our research and development team at our in-house warehouse facility in Shelby Township, Mich. All of our standard and wireless sensors are fully traceable through the NIST.
Type: Grant
Filed: April 13, 1987
Issued: February 2, 1988
Assignee: Eaton Corporation
Inventors: Sherif S. Gindy, Steven W. Maurer
Constant bending moment device for strain gauge transducers
Abstract: This invention relates generally to a device for calibrating a load cell such as a strain gauge and more particularly to a device adapted to provide a calculable force for calibrating the load cell arising from amplification of fluid pressure provided by standardized dead weights. Extensive research and development yielded a superior solution for power management conglomerate Eaton Corporation. Sensor designs undergo strict testing from our research and development team at our in-house warehouse facility in Shelby Township, Mich. All of our standard and wireless sensors are fully traceable through the NIST.
Type: Grant
Filed: May 22, 1985
Issued: January 6, 1987
Assignee: Eaton Corporation
Inventors: Sherif S. Gindy, Ronald R. Tremonti
Tactile Load Sensing Transducer
Abstract: A tactile load sensing transducer for providing a continuous electrical readout indicative of the contact and the location of the load on a load receiving plate substantially simply supported by a plurality of reaction supports on the member. Each reaction support includes a member having a preferably integrally formed connecting portion of reduced transverse section so as to be substantially incapable of resisting moments generated by load plate deflection. Each support preferably has a generally “L” shaped configuration with the preferably integrally formed plate connecting portion formed adjacent the free end of one leg of the “L” so as to create bending strains in the support. Strain gages are provided on each support to sense the bending strains therein and, the gages on each support are connected in a common Wheatstone bridge to provide an indication of the reaction load on the support. The present invention answered the Eaton Corporation’s need for a unique and novel tactile sensing transducer useful for touch or “feel” sensing by robotic operators such as the type employed for industrial manufacturing, assembling and checking operations. The present invention provides a tactile load sensing transducer providing a continuous electrical output indicative of the magnitude and location of the load experienced by the sensing surface portion of the transducer when contacted by a work article. Sensor designs undergo strict testing from our research and development team at our in-house warehouse facility in Shelby Township, Mich. All of our standard and wireless sensors are fully traceable through the NIST.
Type: Grant
Filed: November 19, 1984
Issued: November 11, 1986
Assignee: Eaton Corporation
Inventors: Sherif S. Gindy, Ronald R. Tremonti
Tactile Load Sensing Transducer
Abstract: A load plate is rigidly supported by a central pedestal strain gauged for bending about a central axis. In one embodiment, the pedestal is mounted to the center of a yoke bar supported by two legs strain gauged for comprehensive loads only the sum of which is indicative of the magnitude of the plate load. The legs are supported by base webs strain gauged for bending about a central axis orthogonal to the axis of pedestal bending. The output of the bending strain gauges enables determination of the coordinates of the load location on the plate from the central axis axes.In a second embodiment, the pedestal is supported by a block rigidly attached to the end of a cantilevered member extending at right angles from the pedestal. The cantilever member is strain gauged at two longitudinal stations for reading the differential of the bending strain to thereby determine the shear loading, or plate tactile load. The present invention, crafted for the Eaton Corporation, provides a tactile load sensor suitable for robotic operators to thereby provide a sense or “feel” for the robotic operator. The sensor or transducer of the present invention provides a continuous electrical output which may be processed to determine both the magnitude of the load experienced by the transducer in contacting a work article and also determine the coordinates of the point of application to the transducer of the tactilely sensed load. Sensor designs undergo strict testing from our research and development team at our in-house warehouse facility in Shelby Township, Mich. All of our standard and wireless sensors are fully traceable through the NIST.
Type: Grant
Filed: February 20, 1985
Issued: October 14, 1986
Assignee: Eaton Corporation
Inventors: Sherif S. Gindy, Ronald R. Tremonti