PRODUCTS
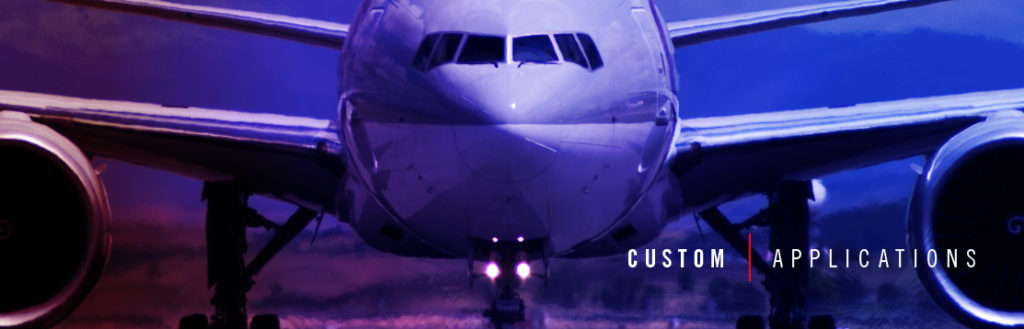
PROJECT:
Aerospace Research and Development for Boeing
Multi-Component Sensor Application
A monolithic company, like Boeing, is a powerhouse in the aerospace industry. The technology the company implements drives creativity and innovation in an expanding field. The success of Boeing’s new designs directly correlates to advancements in the entire industry of flight. Conversely, any obstacles encountered during the research and development or production phases can be extremely detrimental to productivity. This dichotomy is a fine line to walk, especially in regard to Boeing’s new 777X passenger plane. Poised to be the largest and most efficient twin-engine jet in the world, the 777X promises improved passenger room, wider windows, a broader cabin, new lighting and other nuances.
With such enticing features, it’s understandable that Boeing grew frustrated when an overseas contractor they had chosen in India failed to deliver on parts. Not only did this waste Boeing’s valuable development time, it also cost the company thousands of dollars in expenses. Pensive, Boeing sought a more reliable solution. That’s when they discovered our research and development engineers at SensorData Technologies. We quickly went to work coordinating plans with Boeing to help develop a custom multi-component sensor for testing.
Our Custom Sensor Solution
Initially, Boeing’s vision was to have a small capacity force sensor. As with most projects we handle, it transformed into something entirely different. Given that the jet will be subjected to an extraordinary range of environmental and mechanical requirements, our sensor engineers needed to test for a variety of scenarios. After receiving and completing the assigned sensor specs from Boeing, our sensor engineers initiated the testing phase. While optimal results were gathered, the engaging collaboration between our sensor engineers and Boeing’s staff led to a decision to rethink the project. With the prior testing results in-mind, it was agreed that a new dual range multi-component sensor capable of large and small capacities, torque sensing, thrust sensing, tension/compression sensing and dual bridge features was required.
Again, our sensor engineers and research and development team started working to bring Boeing’s new goal to fruition. The newly crafted multi-component sensor was ready for testing just a few weeks later. Similar to the first application, this new multi-component sensor withstood the rigid testing requirements, leaving both Boeing and ourselves pleased. With the research and development phases concluded, our sensor engineers began replicating the multi-component sensor as to fulfill the quantity order placed by Boeing. All the multi-component sensors made for Boeing were produced in-house at our warehouse headquarters facility.
The extensive work we performed for Boeing is not out of the ordinary. Many of our clients approach us with a certain goal in mind, but as the project evolves, different needs arise. Our sensor engineers are experts at identifying areas of improvement. Boeing’s custom sensor project began with just one area of focus. As developments accumulated, the guidance our sensor engineers provided directed the project to include other areas of measurement. The end result was a functioning sensor capable of gathering data that Boeing had not initially anticipated. What had started as a project for a small capacity force sensor bloomed into a large capacity multi-component torque and thrust sensor thanks to the knowledge of our sensor engineers.
Sensor Research and Development
At SensorData Technologies, solving sensor problems is what we do! When Boeing approached us with this massive task our sensor engineers did not shy away. In just eight weeks we took an idea, reformatted it, subjected it to stringent testing and ultimately ended up with a fully functional multi-component sensor that is making the skies safer. Our dedicated research and development engineers will stop at nothing you provide you with a quality sensor solution that adheres to the finest of measurement requirements. If your industry application demands a custom wireless sensor, then SensorData Technologies Inc. is the choicest candidate. All of our sensor products have been Michigan-made since 1992 and are NIST traceable. If you’re interested in a personal sensor consultation, give us a call at (586) 739-4254 or simply fill out our free online quote to get started today!
PRODUCTS
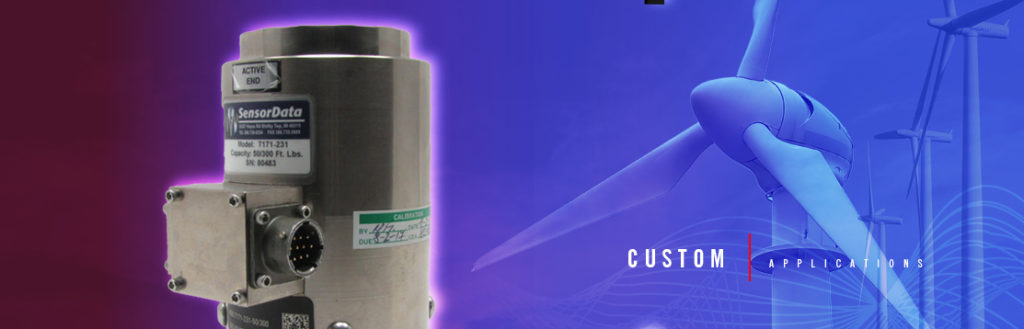
PROJECT:
Fasteners Characteristics under Transverse Loading
A local university prestigious fasteners lab needed some equipment to study the behavior of fasteners under transverse vibration conditions according to DIN 65151. The lab is involved in testing of crucial components for the military, automotive and wind turbine industries and produces high caliber post graduate research on the topic.
Available equipment would either be limited to a narrow size/type of fasteners, or fall short of the number of parameters to be measured.
Solution: SensorData was consulted to design and build a lab quality lest rig which overcomes shortcomings of the state of the art.
The resulting product was a machine that can apply different levels of transverse vibrations to a wide range of fasteners at different amplitudes and frequencies while recording both tightening force on fastener and the transverse load applied.